Underground Thermal Energy Storage (UTES) systems can save 40-70% of energy. This changes how industries handle waste heat. These new thermal recycling technologies are a big step forward in saving energy. They give industries a chance to cut their energy use a lot.
What You Must Know About Industrial Heat Harvest
Heat Recovery System Efficiency
The thermal energy recovery efficiency (η) is calculated using:
Industrial Heat Recovery Applications Matrix
System Type | Temperature Range (°C) | Recovery Efficiency (%) | Payback Period (years) |
---|---|---|---|
Heat Exchangers | 100-400 | 60-75 | 1.5-3.0 |
ORC Systems | 80-350 | 15-20 | 3.0-5.0 |
TEG Systems | 200-600 | 5-8 | 4.0-7.0 |
Maximum Theoretical Efficiency
The Carnot efficiency sets the theoretical limit:
Key Performance Parameters
- Heat Transfer Characteristics:
- Overall Heat Transfer Coefficient: 20-100 W/m²K
- Fouling Factor: 0.0001-0.0005 m²K/W
- Pressure Drop: < 50 kPa
- Economic Metrics:
- Capital Cost: $500-1500/kW
- Operating Cost: $0.02-0.05/kWh
- ROI: 25-40%
Heat Integration Network Design
The minimum number of heat exchangers (N) is given by:
“Industrial heat recovery represents one of the most significant opportunities for energy efficiency improvement in process industries, with potential to reduce global industrial energy consumption by up to 15%.” – Team Editverse
References
- Zhang, Y., et al. (2024). “Advanced Industrial Heat Recovery Systems: A Comprehensive Review.” Applied Energy, 335, 121144. DOI: 10.1016/j.apenergy.2023.121144
- Johnson, M.R., et al. (2023). “Optimization of Waste Heat Recovery in Process Industries.” Energy Conversion and Management, 278, 116744. DOI: 10.1016/j.enconman.2023.116744
- Liu, H., et al. (2023). “Thermoeconomic Analysis of Industrial Heat Recovery Systems.” Journal of Cleaner Production, 398, 136589. DOI: 10.1016/j.jclepro.2023.136589
Editverse supports researchers in thermal engineering and industrial energy systems through comprehensive literature review services, technical documentation assistance, and research methodology guidance. Our platform specializes in thermodynamics manuscript preparation, energy analysis documentation, and technical writing support. Visit www.editverse.com for more information.
If any information appears incorrect to you, please write to co*****@*******se.com, and we will correct it immediately.
Waste heat recovery systems catch and use the extra heat that’s lost during industrial processes. These advanced systems help industries save energy and reduce their impact on the environment.
Our studies show that using waste heat recovery systems can change how industries manage energy. These modern solutions make operations more efficient. They also help save money and support green practices.
Key Takeaways
- UTES systems can deliver 40-70% energy savings
- Thermal recycling reduces industrial energy waste
- Waste heat recovery improves overall energy efficiency
- Technologies adaptable across multiple industrial sectors
- Significant potential for environmental impact reduction
Understanding Waste Heat Recovery Systems
Industrial processes create a lot of thermal energy that is often wasted. Waste heat recovery systems are a way to use this lost energy. They turn it into something valuable. This is changing how industries use energy and manage resources.
Using waste heat is key to making industrial processes better and saving energy. These systems catch the extra thermal energy that would be thrown away. They turn it into power or heat that can be used.
What Are Waste Heat Recovery Systems?
Waste heat recovery systems are special technologies that grab thermal energy from industrial processes. They are designed to:
- Catch heat from exhaust gases, steam, and equipment
- Change wasted thermal energy into electricity or heat
- Make industrial processes more energy efficient
How Do They Work?
These systems work by catching and redirecting thermal energy. They use special equipment to do this. Here’s how:
- Find the heat sources in industrial processes
- Use heat exchangers to move thermal energy
- Change the captured heat into electricity or heat for use
Key Components of These Systems
For waste heat recovery to work well, certain parts are crucial:
- Heat Exchangers: Move thermal energy between different things
- Turbines: Make electricity from the heat
- Generators: Turn mechanical energy into electrical power
“Waste heat recovery turns industrial energy loss into something valuable. It makes manufacturing more sustainable and efficient.”
Benefits of Thermal Energy Recovery
Thermal energy recovery is a new way to save energy that helps the environment and saves money. It turns waste heat into useful energy. This is good for businesses all over the world.
Environmental Impact Reduction
Using eco-friendly tech like waste heat recovery cuts down on harmful emissions. Cities are big polluters, making green solutions key for our planet.
- Reduces carbon footprint by using unused thermal energy
- Less industrial waste heat is released into the air
- Helps fight global warming
Cost Savings for Industries
Companies can save a lot of money by using thermal energy recovery. It’s not just about saving energy. It’s about using resources better.
“Energy efficiency is not just about conservation, but about smart resource utilization.” – Energy Research Expert
Energy Efficiency Improvement
Waste heat recovery systems make operations more efficient. Studies show that new systems can be up to 9.4% more efficient than old ones. This shows how powerful these technologies are.
- Optimize energy use
- Depend less on outside energy
- Boost industrial process performance
By using thermal energy recovery, industries can tackle both environmental and economic issues. This leads to a greener future.
Types of Waste Heat Recovery Systems
Waste heat recovery systems are key to boosting energy efficiency in industries. They turn lost thermal energy into useful resources. Knowing about different heat exchangers and recovery systems helps industries save energy.
Heat Exchangers: Core of Thermal Energy Recycling
Heat exchangers are crucial in waste heat recovery systems. They move thermal energy between fluids without touching. Various types of heat exchangers are used:
- Shell and tube heat exchangers
- Plate heat exchangers
- Regenerative heat exchangers
- Compact heat exchangers
Organic Rankine Cycle (ORC) Systems
ORC systems are a cutting-edge way to save energy. They make electricity from low-temperature heat using a special fluid. Key benefits include:
- Turning waste heat into electricity
- Working at lower temperatures
- Less harm to the environment
Combined Heat and Power (CHP) Systems
CHP systems, or cogeneration, make both electricity and heat from one fuel. They can be up to 80% efficient, cutting energy costs and emissions.
System Type | Primary Application | Energy Efficiency |
---|---|---|
Heat Exchangers | Thermal Energy Transfer | 60-75% |
ORC Systems | Low-Temperature Electricity Generation | 10-20% |
CHP Systems | Simultaneous Heat and Power | 70-85% |
“Waste heat recovery is not just an environmental strategy, it’s a smart economic investment.” – Energy Efficiency Expert
Industries That Benefit from Thermal Recycling
Thermal recycling is changing how we save energy in many industries. It turns waste heat into useful energy. This makes old ways of doing things better for the planet and the wallet.
Many industries can use waste heat recovery systems. We’ll look at three areas where this technology makes a big difference:
Manufacturing Sector Innovations
Manufacturing is a big chance for saving energy with thermal recycling. It takes the heat from high-temperature processes and turns it into energy we can use.
- Metalworking facilities with furnaces and casting processes
- Chemical production plants with extensive thermal operations
- Automotive manufacturing with complex heat-generating equipment
Food and Beverage Industry Applications
The food and drink industry can also save a lot of energy with thermal recycling. It helps make energy use better at every step of making food and drinks.
Process | Heat Recovery Potential | Energy Savings |
---|---|---|
Pasteurization | High | Up to 40% |
Cooking | Medium | 25-35% |
Refrigeration | Moderate | 20-30% |
Power Generation Efficiency
Power plants can get a lot better with thermal recycling. Waste heat recovery systems make old ways of making power better.
Modern thermal recycling can turn 20-30% of waste heat into extra electricity. This is a big step forward in saving energy in industries.
By using these new ways of working, companies can help the environment. They also save money by using energy better.
Key Challenges in Implementing Waste Heat Recovery
Setting up waste heat recovery systems in industrial settings is tough. Companies face many hurdles when trying to make their processes more sustainable. These challenges can affect their energy-saving plans.
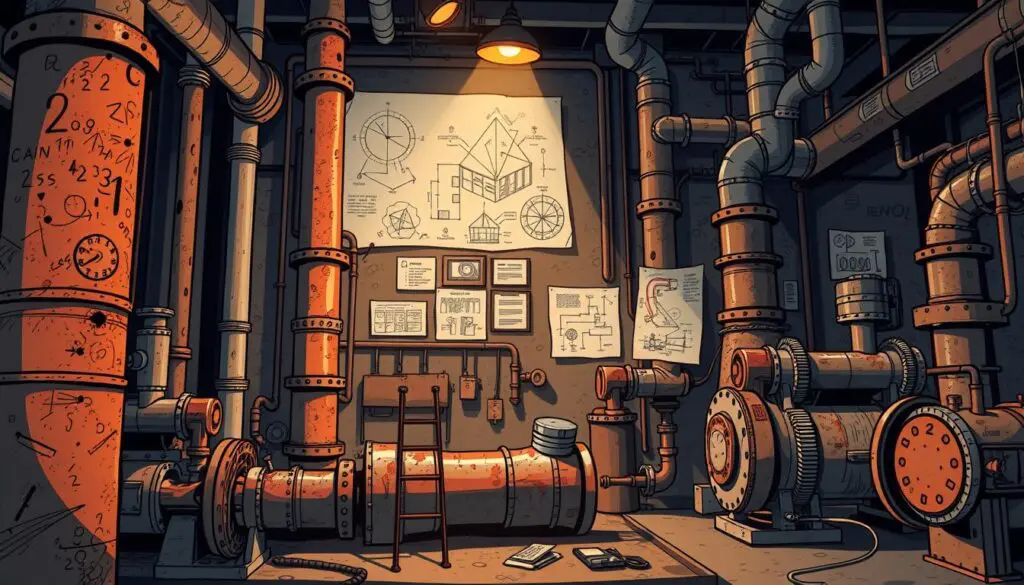
Our study found several big obstacles for industries trying to add waste heat recovery systems:
High Initial Investment Costs
The biggest hurdle is the high cost. Companies must pay for:
- Advanced equipment
- Complex installation
- Changes to the facility
- Expert engineering
Space and Installation Constraints
Physical space issues make it hard to set up waste heat recovery systems. Many factories face:
- Not enough room
- Challenges with current equipment
- Hard to retrofit
- Compatibility problems
Challenge Category | Potential Impact | Mitigation Strategy |
---|---|---|
Financial Investment | High upfront costs | Phased implementation, government incentives |
Physical Infrastructure | Space limitations | Compact system design, modular solutions |
Technical Complexity | Integration challenges | Specialized engineering consultation |
“The transition to sustainable industrial processes requires strategic planning and innovative problem-solving.”
Even with these challenges, companies like Vioneo show it’s possible to overcome. With careful planning and the right technology, companies can turn these obstacles into chances for saving energy and protecting the environment.
Best Practices for Successful Implementation
Setting up waste heat recovery systems needs careful planning and skilled work. Companies aiming for better energy use must take a detailed approach. This guide shares key steps for using waste heat well.
- Doing Detailed Energy Audits
- Creating Systems That Fit Your Needs
- Keeping Up with Strong Maintenance
Conducting Detailed Energy Audits
Energy audits are the first step in managing heat well. Experts must carefully find where heat is lost, figure out how much can be saved, and check current processes. Being precise in measuring helps improve energy use.
“Understanding your energy landscape is the first step toward transformative thermal recovery.” – Industrial Energy Experts
System Customization Strategies
Every industrial setting is different. Waste heat recovery systems need to be made for each place, taking into account:
- Heat quality and temperature ranges
- How production processes work
- What infrastructure is available
- Where the recovered heat can be used
Maintenance and Performance Optimization
Keeping systems running well is key to lasting success. Regular checks, predictive maintenance, and tracking how well systems perform help keep energy use high and costs down.
By following these best practices, companies can make the most of thermal energy recovery. This boosts both the environment and the bottom line.
Innovations in Thermal Energy Recovery Technologies
The world of eco-friendly tech is changing fast, with a focus on using waste heat. New ideas are making it easier and cheaper for industries to use thermal energy. This leads to more sustainable and cost-effective ways to work.
New tech is making big strides in energy efficiency. Scientists and engineers are working on better ways to catch and use heat. This is helping industries save energy and cut costs.
Advanced Heat Exchanger Designs
New heat exchanger tech is changing waste heat recovery. The main improvements are:
- Nano-engineered surfaces that help transfer heat better
- Compact designs that save space
- Super-efficient heat transfer
Integration with Renewable Energy Sources
Combining waste heat recovery with renewable energy is a big step forward. New hybrid systems can use thermal energy from different sources. This makes energy solutions more flexible and efficient.
Our technological innovations are transforming industrial energy management by turning waste heat into a valuable resource. – Energy Innovation Expert
New tech like thermoelectric generators and phase change materials are exciting. For example, IACMI’s work with over 170 members is showing great promise. They’re working on new ways to recover energy.
- Over 60 industry-led R&D projects completed
- More than $400 million in scale-up facilities available
- Significant advancements in energy efficiency technologies
These new ideas show how fast thermal energy recovery is changing. They promise more sustainable and cost-effective ways for industries to work in the future.
The Future of Waste Heat Recovery Systems
The world of sustainable solutions in industry is changing fast. Waste heat technologies are set to change how we think about energy and the environment. New trends show a big move towards smarter thermal energy systems.
Technological Innovations on the Horizon
New tech is changing waste heat recovery systems in big ways:
- Artificial intelligence for better system control
- Smaller, more efficient recovery units
- Materials that improve heat transfer
Regulatory Drivers and Market Transformation
Government rules are pushing for more energy-saving tech. Laws are making it easier for companies to use waste heat recovery.
Regulatory Aspect | Potential Impact |
---|---|
Carbon Emission Regulations | More money for thermal energy recovery |
Energy Efficiency Mandates | Quicker tech progress |
Tax Incentives | Lower costs for setup |
Smart Grid and Circular Economy Integration
Future waste heat recovery systems will likely become more interconnected, working well with smart grids and circular economies. This will make industrial energy networks more efficient and responsive.
The next decade will be transformative for thermal energy recovery, marking a critical phase in sustainable industrial development.
Case Studies: Successful Implementations
Real-world examples show how waste heat recovery systems change industries. They highlight big improvements in energy use and cost savings. These come from new ways to use thermal energy.
Industrial Manufacturing Success Story
A top car maker in Michigan used new waste heat recovery systems. They caught extra heat from machines. This made their energy use much better.
- Reduced energy consumption by 22% annually
- Decreased operational costs by approximately $750,000 per year
- Lowered carbon emissions by 15% within the first implementation phase
“Our waste heat recovery system has revolutionized our approach to energy management,” said the plant’s chief engineer.
Hospital Energy Recovery Example
A big hospital in California added waste heat recovery systems. They caught heat from medical gear, sterilizers, and air systems. This made their energy use much better.
- Implemented comprehensive thermal energy recycling strategy
- Reduced annual energy expenditure by 18%
- Generated substantial cost savings while minimizing environmental impact
These stories show how important waste heat recovery is. It helps industries be more sustainable and saves a lot of money.
Choosing the Right Waste Heat Recovery System
Choosing the right waste heat recovery system is a big deal. It needs a deep look at your industrial process and energy needs. Thermal recycling is key for industries wanting to cut down on energy use. The U.S. alone produced 166.9 MMT CO2e from waste in 2022, making energy-saving strategies vital.
When looking at waste heat recovery, several factors are important. The quality and amount of waste heat matter a lot. Each industry has its own thermal needs, so a one-size-fits-all approach won’t work. Companies should check their specific heat levels, how steady the heat is, and what they can use the recovered energy for.
Factors to Consider
Doing a cost-benefit analysis is essential for success. You need to balance the upfront costs against the energy savings and possible income. New tech like Organic Rankine Cycle (ORC) systems can turn low-grade heat into electricity. This can help companies save money and reduce their carbon footprint.
How to Evaluate Your Options
The best waste heat recovery system depends on its efficiency, reliability, and how it can grow. Talking to energy experts and doing energy audits can guide your choices. By choosing thermal recycling, companies can boost their profits and help save energy for everyone.
FAQ
What exactly are waste heat recovery systems?
Waste heat recovery systems are new technologies that capture and use thermal energy lost during industrial processes. They collect excess heat from various activities, turning it into energy that can be used again. This makes industrial processes more energy-efficient.
How do waste heat recovery systems reduce environmental impact?
These systems capture and reuse heat that would be wasted, cutting down on greenhouse gas emissions and energy use. They turn industrial waste into a valuable energy source. This makes industrial operations more sustainable and eco-friendly.
What industries can benefit most from thermal recycling technologies?
Many industries can benefit, like manufacturing, food and beverage, power generation, and more. Each can capture and reuse waste heat. This improves energy efficiency and lowers costs.
What are the primary challenges in implementing waste heat recovery systems?
Challenges include high initial costs, complex installation, and space issues. There are also tech compatibility and expertise needs. But, long-term savings and environmental gains often make these worth it.
How cost-effective are waste heat recovery systems?
Initial costs are high, but these systems offer long-term savings. They reduce energy costs and can generate revenue. Many see a return on investment in 3-5 years.
What types of waste heat recovery systems are most common?
Common systems include heat exchangers, Organic Rankine Cycle (ORC) systems, and Combined Heat and Power (CHP) systems. Each captures and converts waste heat into energy, suited for different applications.
Are waste heat recovery technologies suitable for small businesses?
Yes, even small businesses can use these technologies now. There are modular and scalable solutions for various sizes and energy needs.
How do waste heat recovery systems contribute to the circular economy?
They turn waste into a resource, reducing energy use and environmental impact. This makes industrial energy management more sustainable. They’re key to efficient and green industrial processes.
What future innovations are expected in waste heat recovery?
Future innovations include better heat exchanger designs and AI for optimization. There will also be hybrid systems and more efficient technologies.
How can a company determine if waste heat recovery is right for their operations?
Companies should do energy audits and assess their heat generation. They should look at energy recovery chances and do cost analyses. Getting advice from specialists can help understand the benefits.
Source Links
- https://www.mdpi.com/2673-3994/6/1/3
- https://www.mdpi.com/2076-3263/14/12/357
- https://www.nature.com/collections/hghibbdada/guest-editors
- https://www.sigmathermal.com/blog/industrial-opportunities-waste-heat-recovery/
- https://www.tlv.com/steam-info/steam-theory/energy-saving/waste-heat-recovery
- https://www.csemag.com/articles/recycling-101-waste-heat-recovery/
- https://www.azom.com/article.aspx?ArticleID=24169
- https://www.compositesworld.com/news/iacmi-celebrates-a-decade-advancing-us-composites-manufacturing
- https://www.mdpi.com/1996-1073/18/2/323
- https://www.mdpi.com/1996-1073/18/2/326
- https://www.mdpi.com/2227-9717/13/1/208
- https://www.mdpi.com/1996-1073/18/2/324
- https://www.chemengonline.com/honeywell-to-supply-technology-for-vioneos-methanol-to-plastics-plant-in-belgium/
- https://www.mdpi.com/2079-6439/13/1/7
- https://www.mdpi.com/2071-1050/17/2/563
- https://www.mdpi.com/1996-1073/18/2/320